Chemical
Chemical industry is embracing emerging technologies such as AI, IoT and others mainly to enhance customer engagement and operations.
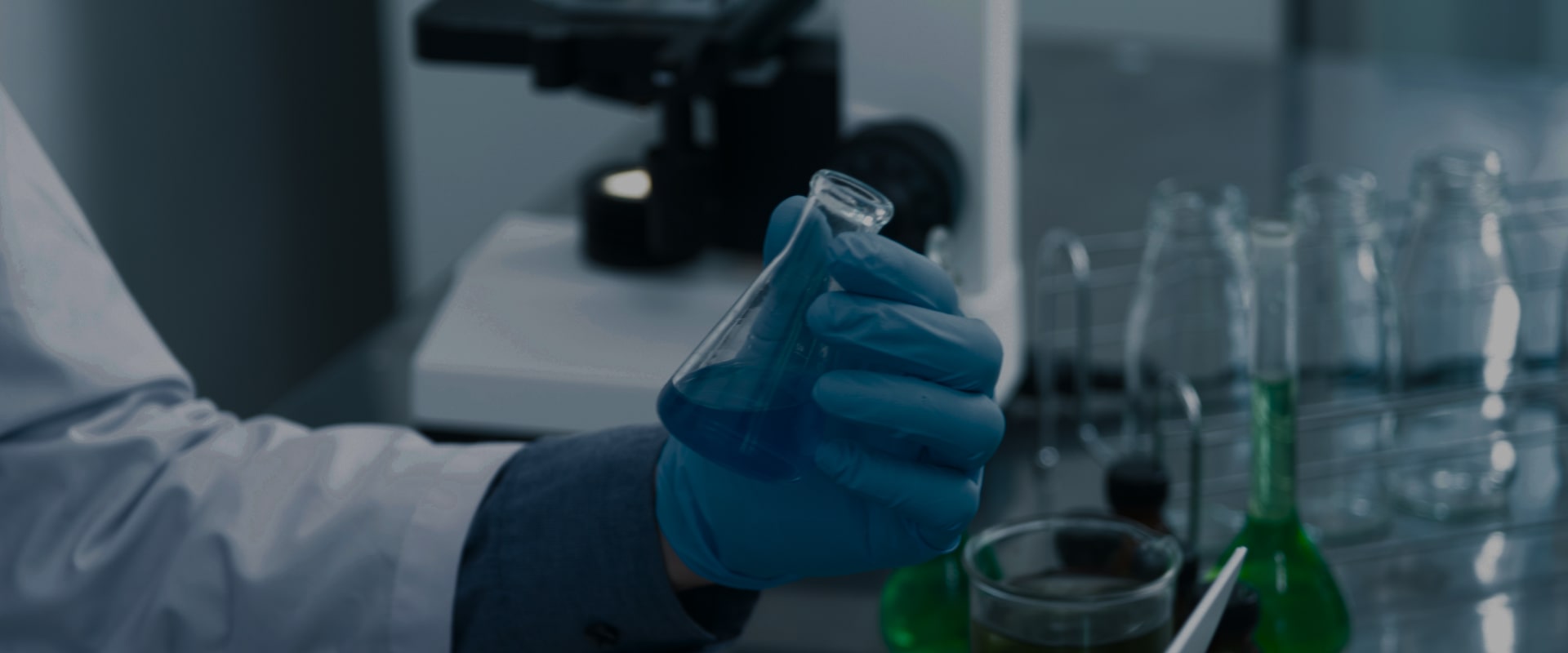
The chemical industry is embracing emerging technologies such as AI and IoT, primarily to enhance customer engagement, operations, and fuel innovation. With AI-enabled supercomputing, the industry is shifting its IT spending towards innovation and value creation. Businesses in the chemical sector are discovering new market opportunities as more prospects connect to the internet, fostering increased connections between businesses and suppliers through digital channels.
Traditionally, chemical manufacturers identified product quality issues after production, relying on experienced employees to manually compare production data against various benchmarks. However, deep learning algorithms can detect problems early by analyzing input data, such as quantity and type, along with real-time production factors like temperature, pressure, and flow. Approximately 85% of production problems stem from normal variations, which AI can help control and adjust to optimize yield. This automated approach is a substantial improvement over human-led manual operational adjustments, resulting in a consistent and predictable yield, increased quality, and revenue.
Chemical manufacturing is highly dependent on external factors like temperature and pressure. Sensors capture these operational variables, tracking them over time and comparing them against outputs to create predictive models. AI can then use this data to prescriptively optimize settings before the manufacturing process begins and make real-time adjustments as necessary, such as changing the rate of flow or condenser temperature. This automated process is more effective than human-led manual adjustments, which are reactive and rely on intuition and experience.
Being one of the world’s most tightly regulated industries, chemical manufacturing adheres to a mix of national and international protocols governing core operational procedures, health, safety, and environmental (HSE) factors. By combining Industrial Internet of Things (IIoT) technologies, real-time data collection, and advanced analytics, AI improves personnel safety, protects physical assets, and ensures compliance with regulatory requirements related to data collection and documentation. Sensors and machine-augmented data capture information from the physical world, transforming it into a digital record of operations and supply networks. This monitoring data enhances visibility of assets and personnel, even at remote sites. When fully integrated, AI can identify issues ranging from employees not wearing proper PPE to leaks and other environmental hazards.
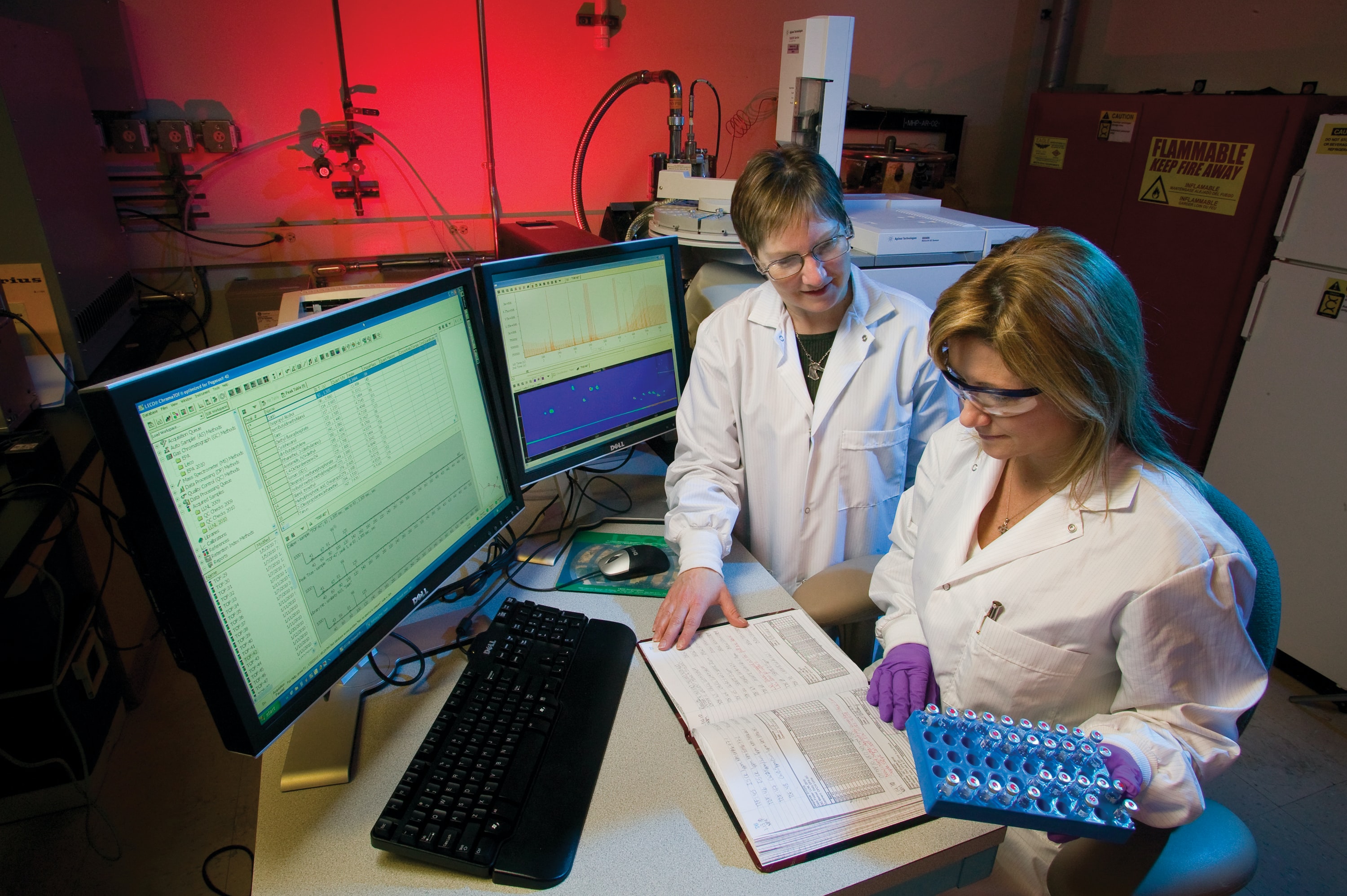
Product Development
Various regression and classification techniques prove effective in accurately predicting the properties of hypothetical molecules, aiding researchers in synthesizing only the most promising ones. Subsequently, similar models can be applied to forecast the outcome of a given reaction, along with the necessary conditions for that reaction to occur.
Product Design
Designing new molecules traditionally relies on deep domain knowledge and creativity. However, emerging deep learning algorithms overcome inherent limitations of the human mind. These algorithms support researchers by rapidly generating large numbers of molecules in a short period, and when well-constructed, they exhibit less bias than human creativity.
Product Optimisation
The quest for optimal reaction conditions often involves numerous synthesis trials and errors, especially when dealing with a significant number of adjustable parameters to control. Recurrent neural networks expedite this extensive process by iterating over all possible parameter combinations, swiftly identifying an optimal solution based on your target.
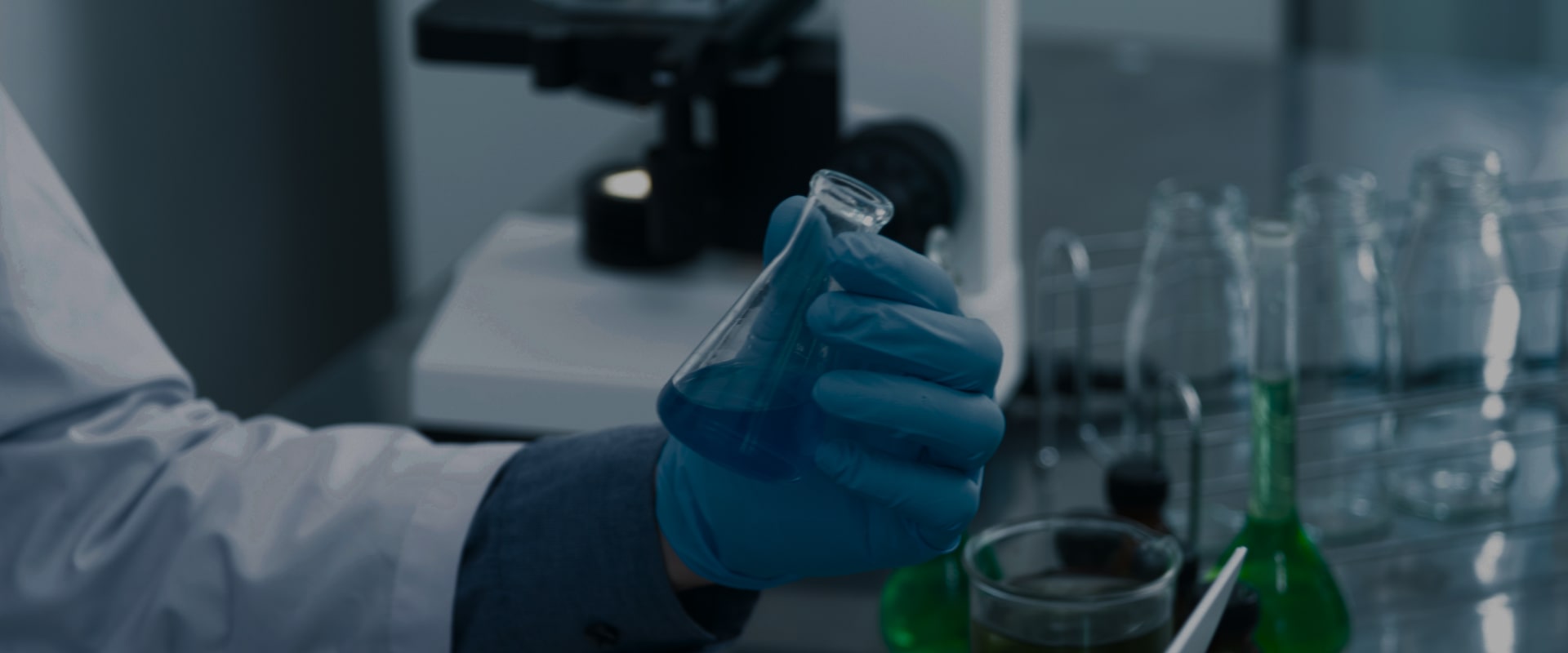
Automated Root Cause Analysis
Conducting Automated Root Cause Analysis provides a swift and accurate insight into process inefficiencies. This methodology enhances historical and real-time asset data, applying machine learning algorithms to automatically trace the causal chain of events leading to production failures. Once process inefficiencies are identified through analyzed data, translating this information into insights is crucial. Industrial Predictive Analytics comes into play for this purpose, where machine learning algorithms are implemented to identify relevant events and predict their outcomes. The implementation of process-based machine learning allows manufacturers to receive focused and contextual predictive alerts. This is particularly advantageous for chemical manufacturers, given that operational technology (OT) data is already well-organized and captured within data historians. By leveraging this data with process-based AI, manufacturers can precisely pinpoint the root cause of process disturbances and predict process instabilities and failures before they impact production. Incorporating AI as part of a broader digital reinvention strategy, investing in select functions, and developing organizational capabilities are crucial for realizing value in the enterprise. According to survey responses from industry leaders, chemicals and petroleum organizations should strategically consider digital technologies, leverage analytics and AI across the business, capitalize on data, and establish data governance to fully exploit the potential of AI.